
Furthermore, knowing the properties of a single cell is a key feature when integrating topology optimization in the design workflow and also for applying the homogenization method during the mechanical characterization of lattice structures.Ī 1 mm unit cell of P-Surface type was modeled as described in. The findings show the accuracy of the proposed modeling method more, the numerical model allows to relate the thickness of the part to the mechanical properties by simulating a single cell inside the lattice structure, saving computational time, and giving directions for tailored applications with lattices that present variable properties in the design volume. As a result, a model of mechanical properties as a function of the cell relative density is proposed and compared to the ones available in literature. Nevertheless, the geometrical accuracy of the modeling method and the mechanical characterization of the thickened structure still need to be investigated.Īs an extension of the aforementioned work, in this study, the geometrical deviation of the subdivided TPMS P-Surface from the implicit defined one is investigated, then the mechanical properties of the unit cell are computed by finite element analyses. To overcome these limitations, a novel method for geometric modeling variable thickness triply periodic surfaces based on a subdivision surface algorithm has been recently proposed. As emerged in recent studies, current mesh or parametric models are not ideal for modeling lattice structures, due to the significant computational resources required, processing times, robustness, rendering and visualization issues.
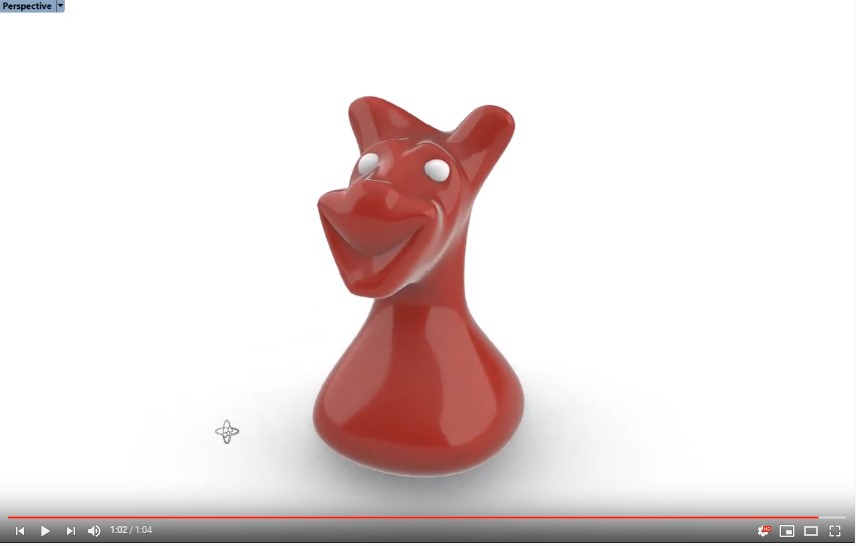
TPMS can be modeled adopting different methods: boundary representation (BRep), volume representation (VRep) and constructive solid geometry (CSG). Furthermore, due to their curvature continuity, the stress concentration at nodal points is eliminated and fatigue life is improved compared to beam-like lattice structures. These surfaces have received huge attention in the research community due to their intrinsic properties, especially in the biomedical field, where it is mandatory to use porous scaffolds designed to allow fluid exchange and tissue regrowth. Minimal surfaces repeating themselves in three dimensions are called triply periodic minimal surfaces (TPMS). Minimal surfaces are a kind of lattice structures defined as surfaces with zero mean curvature or surfaces that minimize the surface area for given boundary conditions.

Lattice structures, indeed, can find application from microscale to macroscale, from tissue engineering, to construction. Among the lightweight structures, cellular solids or lattice structures are characterized by superior properties: they have high specific stiffness and strength, and they are good heat exchangers, energy absorbers and acoustic insulators. Nevertheless, anisotropic materials, surface finish, costs and security are just some of the open issues. The spreading of additive manufacturing (AM) technologies makes it possible to produce parts with unprecedented complexity, such as biomimicry products, organic shapes and lightweight components.
